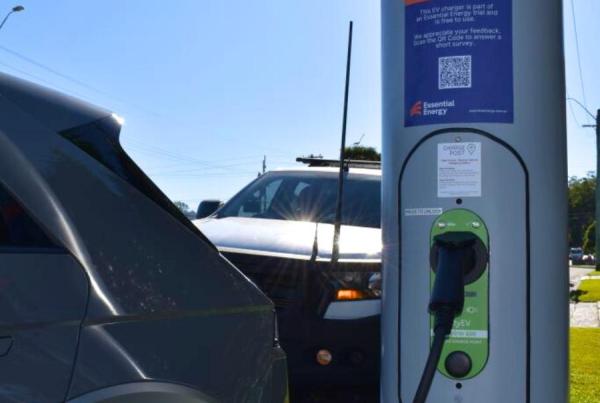
Fibre Reinforced Polymer (FRP)
Wagners Composite Fibre Technologies (CFT) engineer & manufacture a wide range of innovative solutions for civil engineering projects
EXPLORE ALL OF OUR COMPOSITE SOLUTIONSWagners CFT manufacture innovative structural composite sections using a unique pull-winding process that can be used as a replacement for steel, aluminium and wood in infrastructure projects or engineering applications. Our Fibre Reinforced Polymer (FRP) has significant advantages compared with traditional building materials as it is resistant to corrosion, lightweight yet strong, easy to install and maintain.
We proudly work with…
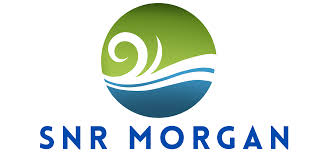
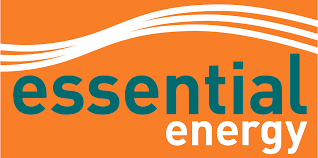
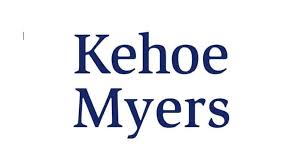

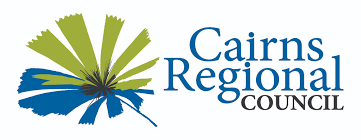
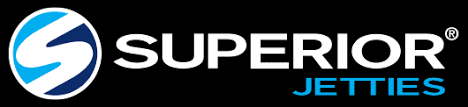
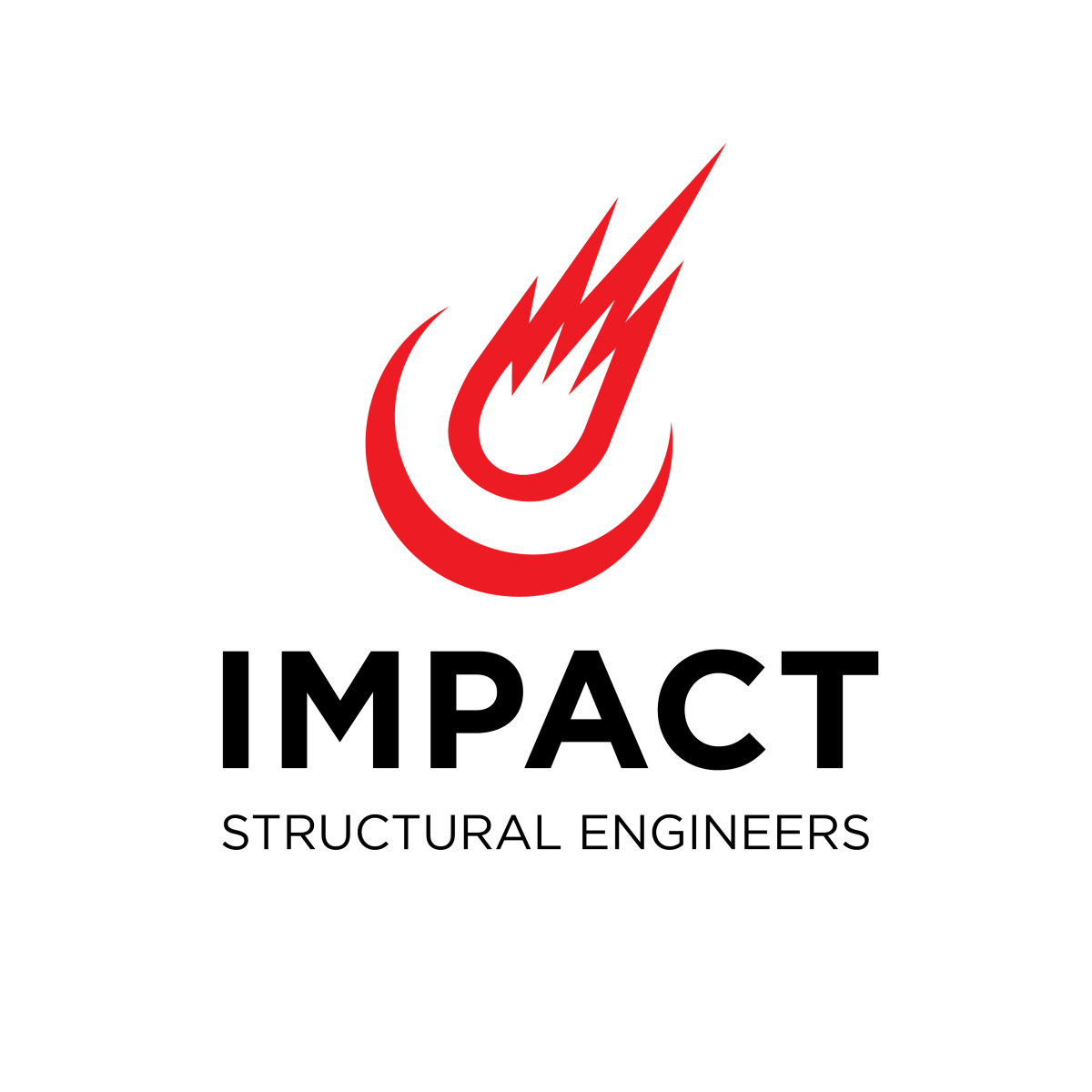
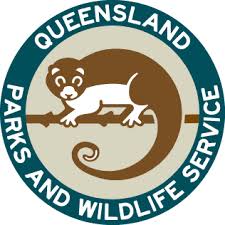
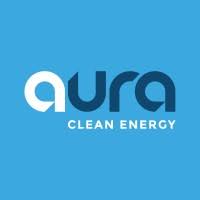
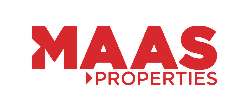
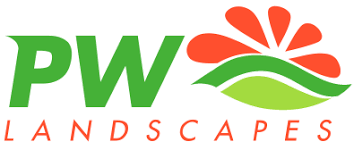
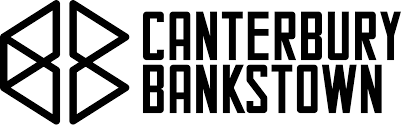
Fibre Reinforced Polymer (FRP) Construction – FAQs
What resin is used in Wagners CFT?
At Wagners CFT, our FRP is manufactured from fibreglass reinforcements and vinyl ester resins. VE resin has been selected over unsaturated polyester and epoxy resin because it provides strength and chemical resistant properties similar to epoxy resin with a significant cost advantage.
Is it polymer or plastic?
Fiber reinforced polymer (FRP) is sometimes also known as fibre reinforced plastic. Both are the same idea of a composite material made up of a polymer matrix reinforced with glass fibres. Fibre reinforced plastics are essentially similar to our FRP material, however, our ratio of glass fibres (at 76% glass) is the reason we refer to our composite product materials as fibre reinforced polymers. At Wagners CFT, these are our fibre materials – we do not use carbon fibres in our manufacturing process.
A composite polymer is one that results from bonding two or more homogeneous materials (each with its own different material properties) in order to create a new final product that has particular desired material and mechanical properties.
What are the production processes used in FRP fabrication?
At Wagners CFT, we use what is known as a pultrusion process. Pultrusion is the pulling of material, such as fibre and resin, through a shaped die. The pultrusion process starts with racks holding rolls of glass fibre roving. These glass strands are pulled off the racks and guided to the necessary shape, orientation and layers before entering a resin injection system.
A surface veil is incorporated to improve surface finish and provide resistance to Ultra Violet (UV) degradation. The fibre reinforcement becomes fully injected (wetted-out) with the catalysed resin such that all the fibre filaments are thoroughly saturated with the resin mixture.
This wetted fibre then enters the heated curing die. The heat initiates a chemical reaction in the resin which causes it to harden and the finished profile exits the die and is subsequently cooled.
What is used as FRP materials?
The fibre reinforcement material used by Wagners CFT is glass fibre. This raw material ensures stronger, stiffer reinforcing filaments. The glass fibers are pulled through and injected with vinyl ester resin. These materials are then heated to become the solid FRP. We also use a fluoropolymer paint system to provide a range of colour options and essentially block ultraviolet radiation from the surfaces of our FRP sections.
Can FRP be used as rebar?
Various materials are increasingly being adopted for use in reinforced concrete instead of steel rebar. These alternatives include steel or carbon fibers, carbon fiber cables, fiber reinforced polymer (FRP) rebar, and even bamboo. Notably, FRP rebar is gaining popularity as a substitute for steel reinforcement due to its non-corrosive nature, lightweight properties, and non-conductivity. These attributes make FRP rebar particularly durable in corrosive environments, easy to transport and install, and advantageous for electrical applications.
How long will FRP materials last in a construction application?
FRP is incredibly durable and inert, and in most construction applications, FRP structural members have a 100-year design life. In some applications, such as Marine Trident Piles, the expected design life is 50 years. For utility poles, FRP has an expected 80-year design life, which is considerably longer than traditional materials and with lower maintenance needs.
What sections are available in FRP from Wagners CFT?
We make our FRP polymer sections as standard structural section in the following:
- Circular hollow sections
- Square hollow sections
- Rectangular hollow sections
- Flat sections
- Bonded structural sections (Bonded I sections, bonded u sections, bonded square sections and bonded rectangular sections)
For precise details and measurements on all sections available, see our product guide.
Is FRP a recyclable material?
One of the main sustainability challenges with FRP is its recyclability. Unlike metals, which can be easily melted down and reused, FRP composites are more difficult to recycle. The process to separate the fibres from the polymer matrix is complex and not widely implemented.
While traditional recycling is challenging, FRP waste can sometimes be repurposed or downcycled into less critical applications. Advances in recycling technologies are being researched to improve the recyclability of FRP materials.
Is FRP a sustainable alternative?
In certain applications, such as bridge construction or retrofitting, the use of FRP can lead to significant energy savings over the structure’s lifetime due to its durability and reduced maintenance needs.
In environments where corrosion and harsh weather conditions are a concern, the use of FRP can prevent the environmental impact associated with the frequent repair and replacement of traditional materials.
FRP materials are highly durable and resistant to corrosion, chemicals, and environmental degradation. This means structures made with FRP often have longer lifespans and require less frequent replacement or repair compared to traditional materials like steel and concrete.
The reduced need for maintenance and repair over the lifecycle of FRP components also results in fewer resources being used for upkeep, which contributes to overall sustainability.
Is FRP an environmentally friendly choice?
The raw materials we use at Wagners CFT in FRP construction, which are glass fibres, are generally less environmentally damaging compared to other options such as carbon fibres.
While FRP is not without its environmental challenges, particularly concerning its production and end-of-life recycling, it offers significant sustainability benefits in terms of durability, reduced maintenance, and overall lifecycle performance. Advances in materials science and recycling technologies are likely to enhance the sustainability profile of FRP in the coming years, making it an increasingly viable option for sustainable construction.
Wagners CFT’s own independently verified Environmental Product Declaration (EPD) gives asset owners the tools to be able to calculate the environmental impact of a project and contribute toward decarbonisation in construction by choosing to use products with reduced global warming potential – such as Wagners FRP – while at the same time meeting your own carbon reduction targets. Find out more about Wagners’ EPD.
What are the options for supplying FRP products to a site?
Wagners CFT’s composite structures can be supplied to site via the following options:
- Pre-assembled
- Partial pre-assembly
- Kit form
- Full on-site assembly
KIT FORM
This option requires a higher level of construction expertise as there is potential for cutting, drilling, and inserting on-site. For this option, Wagners CFT will aim to provide as many members as possible cut to size, pre-drilled, inserted, and glued, however due to possible site variables such as final pile layout, some of these processes may need to be completed in-situ. All members supplied as part of this option will be labelled with the corresponding member ID to match the construction drawings for ease of installation.
This option lends itself well to the installation of boardwalks where members are typically smaller and can be moved without the aid of large machinery. Wagners complete most of the manual work in the factory which greatly reduces the time on-site and ensures all components are installed with ease.
PRE-ASSEMBLED
This is the most efficient option of supply if there is accessibility for a loaded truck and crane. Products such as road bridges, pedestrian bridges, decks and beams will mostly arrive at site assembled and ready for a quick and easy installation ensuring minimum community disruptions and reduced time on-site.
Transport of components to site can be arranged with Wagners CFT utilising our in-house transport fleet. By request, we can supply a site crew to take care of all facets of fitting of the composite structure.
PARTIAL PRE-ASSEMBLY
Larger composite structures may need to be transported in a partially pre-assembled state whereby portions of the structure are assembled by the Wagners production team but still require final assembly and installation on-site. Typically, long span bridges or large wharf projects will come in this form due to transportation restrictions.
FULL ON-SITE ASSEMBLY
This option requires the highest level of on-site support and experience compared to the other options listed above. Composite members, inserts, bracketry and hardware are delivered to site and will require cutting, drilling, inserting, and assembly by the installer. The Wagners design ensures this process is easily completed by individuals with a good knowledge of building and construction.
How is FRP installed at a construction site?
FRP components in construction projects are installed through several methods. Many FRP components are prefabricated off-site and then assembled on-site, which facilitates easier and faster installation.
With Wagners CFT on your team, you will have full access to qualified installation partners who have been trained by our inhouse team at Wellcamp in Queensland. Or we can meet you at your site to provide training and support during the installation process.
Access our Installation Guide to learn all the details, right down to splicing piles, cutting, riveting, drilling, inserting and bolting connections and more.
Which construction industries are already using FRP?
Fibre Reinforced Polymer (FRP) is widely used across various construction industries due to its advantageous properties. Here are some of the key industries already incorporating FRP in their construction works:
Civil Engineering and Infrastructure
- Bridges: FRP is used in the construction and reinforcement of bridges, providing corrosion resistance and reducing maintenance needs. It is used in bridge decks, beams, and as a reinforcement for concrete structures.
- Tunnels: FRP materials are used for tunnel linings and reinforcement, offering lightweight and durable solutions.
Building Construction
- Structural Components: FRP is used for beams, columns, and panels in both residential and commercial buildings, offering high strength-to-weight ratios and design flexibility.
- Reinforcement: FRP sheets and wraps are used to strengthen and retrofit existing structures, improving their load-bearing capacity and extending their lifespan.
Marine and Offshore
- Marine Structures: FRP is ideal for piers, docks, and waterfront structures due to its excellent resistance to saltwater corrosion.
- Boat and Shipbuilding: FRP is commonly used in the construction of hulls, decks, and other structural components of boats and ships.
Transportation Infrastructure
- Highways and Roads: FRP is used in the construction and repair of road surfaces, guardrails, and sound barriers, providing durability and resistance to environmental degradation.
- Railway Infrastructure: FRP components are used in railway sleepers and other structural elements, offering long-lasting solutions with reduced maintenance requirements.
Water and Wastewater Treatment
- Tanks and Pipes: FRP is used for tanks, pipes, and other components in water and wastewater treatment plants due to its chemical resistance and durability.
- Reinforcement: FRP is used to strengthen existing concrete structures in treatment facilities, enhancing their performance and longevity.
Energy and Utilities
- Wind Turbine Blades: FRP is a primary material used in the manufacture of wind turbine blades, providing high strength and lightweight properties.
- Utility Poles: FRP utility poles are used as a lightweight, non-conductive, and corrosion-resistant alternative to traditional materials.
Aerospace and Defence
- Aircraft Components: FRP is used in the construction of various aircraft components, such as fuselage sections and wing assemblies, due to its high strength-to-weight ratio.
- Defence Infrastructure: FRP materials are used in the construction and reinforcement of military structures and facilities, offering enhanced durability and performance.
What is FRP meaning in construction and materials?
FRP construction means using an alternative material to steel, aluminium and timber, that is just as strong and even more durable. With a shortage crisis in supply of some building materials, there’s never been a better time to start considering the alternatives – especially when they come with so many added benefits.
Why choose FRP over conventional materials?
FRP is being chosen over other construction materials because of factors that are undeniably better. Unlike steel, FRP has natural corrosion resistance and does not rust. Unlike timber, FRP composites do not rot and are resistant to termites.
Are there any differences in designing with FRP over steel?
Because Wagners CFT’s pultruded FRP products have different properties to other materials such as steel, allowance needs to be made in design for greater flexibility in bending, concentrated transverse loads and bearing of bolts in holes.
Have a project in mind?
Book a project deep dive with us and work through your projects plans and problems with the experts!