Testing on structural members installed in a highly corrosive marine environment have shown that Wagners Composite Fibre Technologies (CFT) pultrusion maintained its structural strength and continued to meet design values after more than a decade in service.
Cameron Rocks fishing and viewing platform located on the Brisbane River in Hamilton, Queensland posed significant durability challenges for Brisbane City Council due to strong tidal water cycles, highly corrosive salinity and UV exposure.
Pictured – Cameron Rocks is located in Hamilton on the Brisbane River.
In 2009 the old, corroded metallic project was replaced with a more durable Fibre Reinforced CPolymer (FRP) structure.
Wagners CFT LeadStructural Engineer, Dr. Ali Mohammed said twelve years on from project completion and major flooding in 2011, several members were removed for durability investigations and replaced with new ones as part of Wagners CFT’s ongoing Research and Development work.
“Several coupons were cut out from the obtained samples for physical and mechanical testing including interlaminar shear, compressive and flexural strength,” Ali Mohammed said.
“With the interlaminar shear strength under standard ASTM D2344 our test produced a 50.15 MPa result which is in excess of Wagners QA pass mark of 50 and well above the design value of 44,” Dr Mohammed said.
“Meanwhile with the Compressive Strength test under standard ASTM D6641 we achieved a 520.78 MPa result, which again is well above Wagners QA pass mark of 500 and the design value of 485,” he said.
“Finally Flexural Strength testing under standard ASTM D79 produced a result of 890.08 MPa, which is greater than Wagners QA pass mark of 800.”
Barcol hardness testing was also undertaken.
“Barcol hardness was also carried out on the obtained samples and compared with controlled samples and the current QA passmark to evaluate the paint and surface properties,” Ali Mohammed said.
“What we found was that the samples still met the requirements with a slight increase in value which could be attributed to additional curing overtime,” Dr Ali Mohammed said.
“These results really reflect the excellent durability performance of Wagners FRP composites as it demonstrates its high mechanical strength and endurability despite challenging environments which ordinarily would significantly impact the performance of more traditional materials in the same time frame,” he said.
“The results were not a surprise for Wagners because all products are rigorously tested in accelerated durability lab experiments; but what these tests do confirm for us in real life applications is that the verified laboratory simulations are accurately predicting the performance and design life of the members.”
The team reviewed results against water quality in the Brisbane River captured through the Brisbane Airport Water Quality Report from 2002 – 2005.
“From 2002 to 2005 salinity results for the Brisbane River near Cameron Rocks fluctuated around 34g/L; which is in line with what you would expect to see as an average in seawater especially given this area is near the mouth of the river,” Ali Mohammed said.
“As we saw with the structure which was replaced in 2009, corrosion of reinforcing steel and other ferrous metal is one of the biggest causes of deterioration in coastal construction projects,” Dr Mohammed said.
“Certainly in a twelve year period should we have built that structure with metal again instead of FRP I expect that we would have found similar results to the structure which was replaced in 2009 because the bacteria in ocean water consumes iron and their excretions turn to rust making metal projects problematic from a sustainability/durability point of view,” he said.
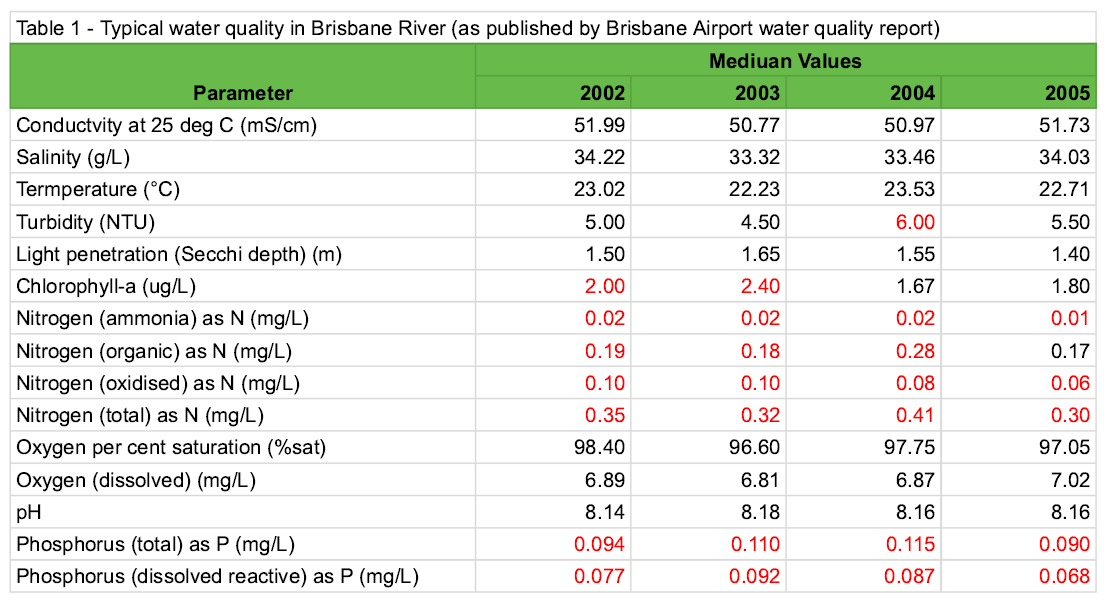
Wagners FRP is one of the lightweight structures commercially available and well known for high performance in high-stress and chemical environments.
“The state of the art design and manufacturing of Wagners FRP composites delivers exceptional chemical and mechanical properties that can withstand harsh environments,” Ali Mohammed said.
“Our FRP sections are used in various applications ranging from high-stress, electric and thermal environments like electric poles to support structures for construction industries,” Dr Mohammed said.
“The high fibre volume fraction allows our composites to withstand extreme conditions without demonstrating any failures,” he said.
“The fact that these members are manufactured here in Australia, to Australian standards for Australian conditions also certainly goes a very long way to ensuring that structures constructed from these members will perform beyond expectation and showcase exceptional durability.”
To view Wagners CFT’s range of products and better understand the performance advantages of construction with FRP visit Product Guide.