Thinking beyond what you’ve been told is achievable, and proving the impossible is actually possible was inducement enough for a group of engineers at Wagners Composite Fibre Technologies (CFT), to deliver the longest riveted Fibre Reinforced Polymer (FRP) truss bridge in Australia; possibly the world!
At 18 metres long and 2 metres wide, the heritage green pedestrian bridge now sits unassumingly over an ephemeral creek west of Proserpine on the central Queensland coast; just down from the lawn bowls club on Scottsville Road in Collinsville.
Wagners CFT Lead Structural Engineer Dr Ali Mohammed said for the tiny township of 1,200, the bridge’s installation was probably fairly uneventful for Collinsville; but for him and his colleagues the bridge represents pushing beyond the threshold of design limitations and challenging long-held beliefs and norms.
“Breaking records is always unique and at 18 metres long the Scottsville Road pedestrian bridge in Collinsville is about 2 metres longer than any other riveted FRP truss bridge in Australia; possibly the world,” Dr Ali Mohammed said.
“It was designed in house here at Wagners CFT by our design team and certified externally by Impact Structural Engineers,” Dr Mohammed said.
“The bridge was pre-assembled at Wagners CFT in Wellcamp before being trucked some 1,100 kilometres up the Leichhardt Highway to Collinsville and craned into place ahead of final installation by local contractors PW Landscapes,” he said.
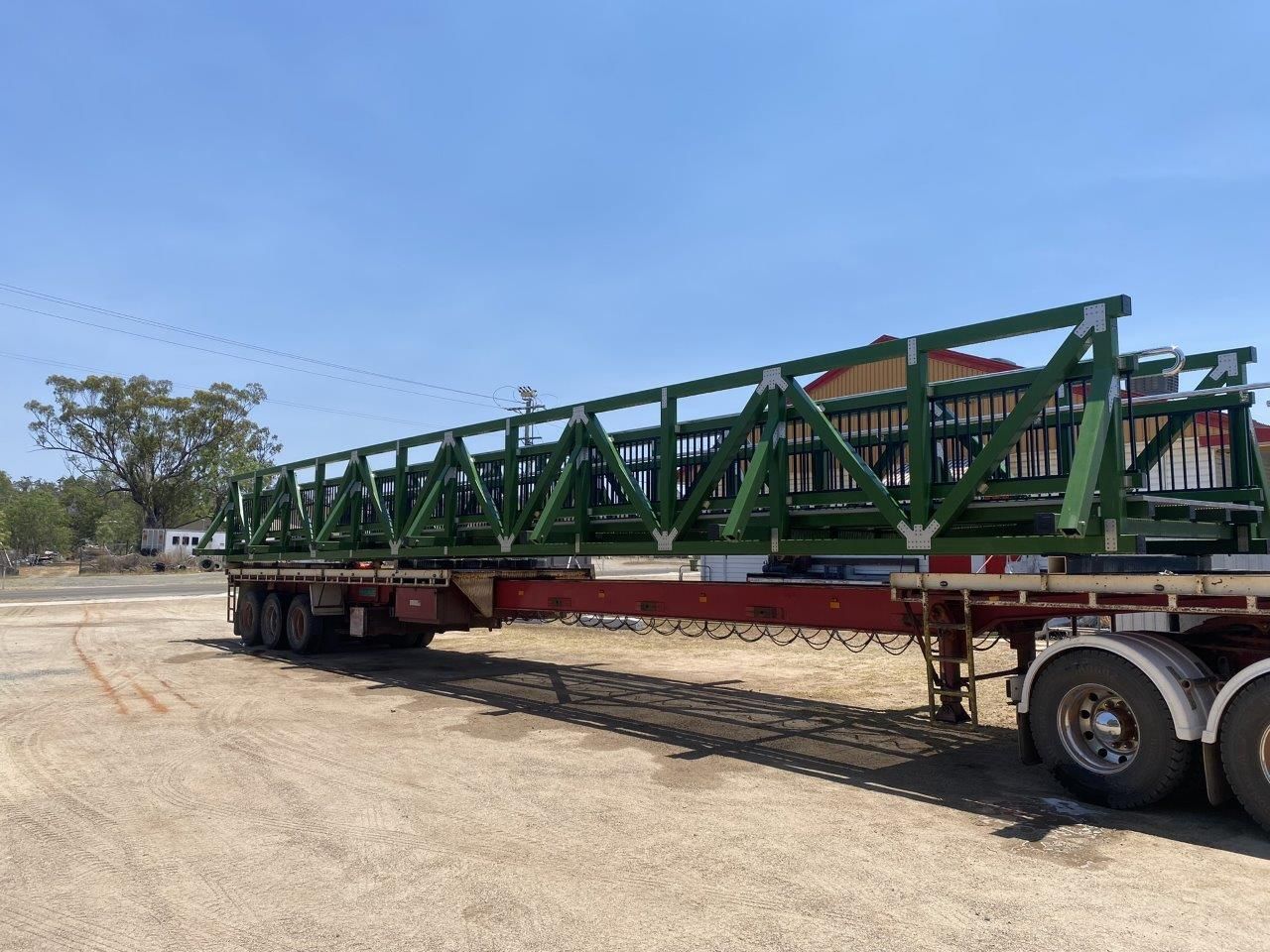
Pictured – The bridge was pre-fabricated at Wagners CFT in Wellcamp, Qld before traveling some 1,100km to Collinsville, Qld.
Fifteen to sixteen metres has traditionally been the design threshold for a riveted truss bridge like this.
“From a design perspective and at 18 metres, normally we would need to have gone with bolted 125 SHS sections because it’s a heavier bridge; heavier in design,” Ali Mohammed said.
“But we have used 125 SHS sections for top and bottom chords and webs and with detailed design checks on serviceability limits, vibrations and riveted connections, we were able to work with Wagners R&D team on the Young’s Modulus of the material and the riveted connections and push the design to 18 metres,” Dr Mohammed said.
“Every FRP truss bridge is challenging to design mainly due to vibration and for this bridge the challenge was to keep the natural frequencies and acceleration ranges within the pedestrians comfort limit according to the design code,” he said.
“This was a big challenge and we achieved this by adopting adequate truss stiffness, considering the elastic modulus of the material being Wagners CFT FRP and the depth of the truss; you want to maintain usability, you don’t want to go so high that you lose aesthetics or usability of the bridge.”
Pictured – The deck of the new FRP riveted truss bridge is 30mm FRP mini mesh.
Riveted truss bridges are more cost effective because they are lighter and require less material.
“Riveted truss bridges are lighter in weight and easier to build and install compared to bolted truss bridges as they are considered light duty bridges,” Dr Ali Mohammed said.
“The advantages of using a riveted FRP truss bridge is that it is more cost-effective as you use less material, use lighter connections and its overall lighter weight so it is quicker to fabricate and install,” Dr Mohammed said.
“It still meets the same design load and design life of 100-years, everything else is the same; just the cost for the asset owner and ease of installation is better,” he said.
“I am very proud of this bridge being the longest riveted FRP bridge in Australia because we’ve proven that you do not have to be limited by predetermined boundaries and that providing the numbers add up…it’s possible!”
Meanwhile Owner of PW Landscapes Matt Stokes said a bridge like this is just plug and play for them.
“The design process for us was good and from our perspective it’s made our job very simple; you just have to do an abutment to suit, drop in the edge and then you just have a small two metre tie in,” Matt Stokes said.
“It’s plug and play for us and a fantastic way to do it to minimise the amount of time you are on the work site,” Mr Stokes said.
“It’s the only way to do a pedestrian bridge if you have access for cranage and someone who can pre-fabricate the bridge off site instead of building it over rocks and dust,” he said.
“Time wise it is three to four weeks quicker when you get the bridge built in a workshop at factory rates, in a controlled environment, by a team who work with the product all the time; making it cheaper, more efficient and quicker.”
“Rather than three or so blokes on site for three to four weeks, paying accommodation and meals.”
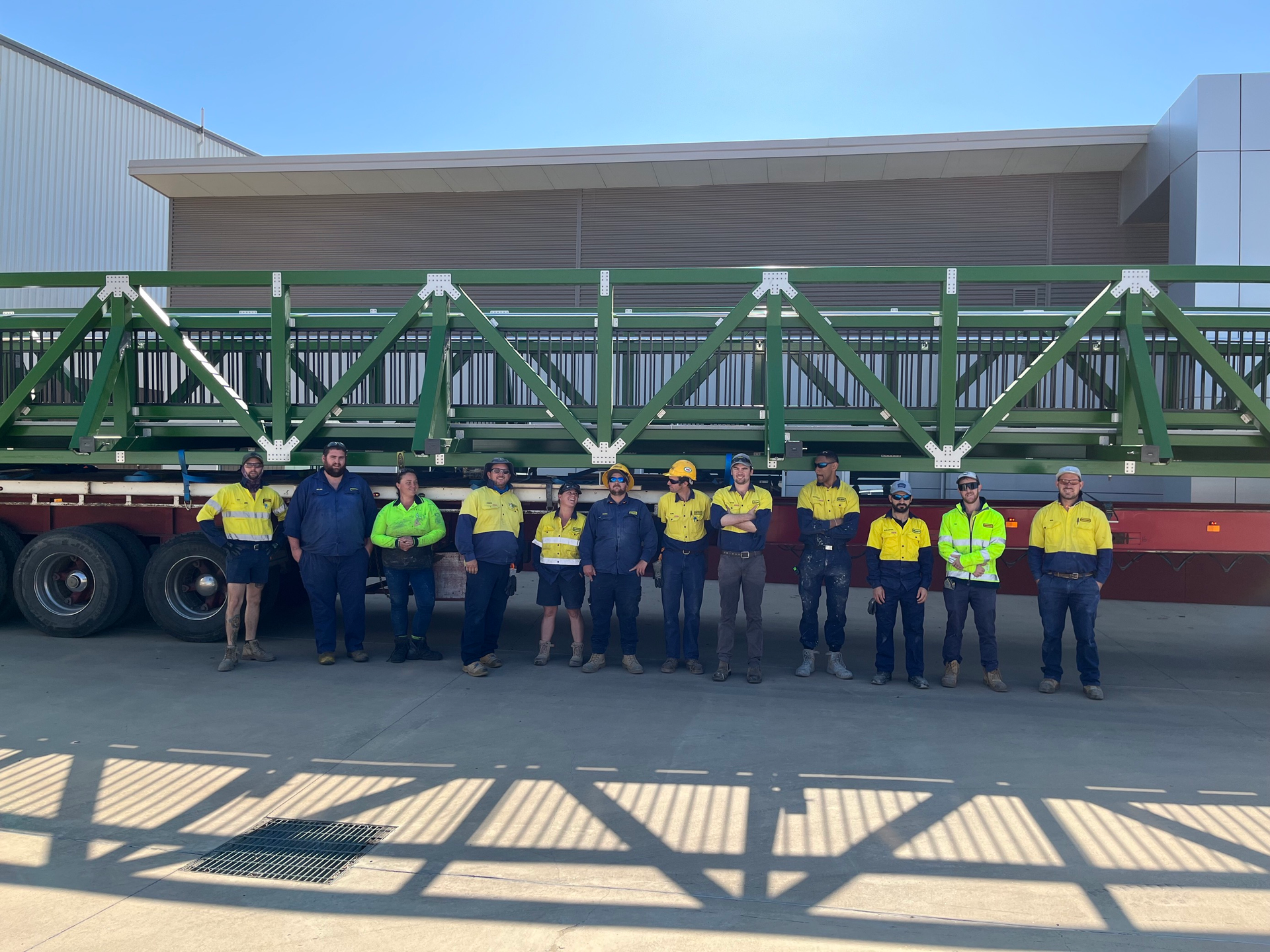
Pictured – The team at Wagners CT who prefabricated the bridge off site for PW Landscapes.
For waterways the truss bridge is preferred by PW Landscapes because it doesn’t have any foundations that impede natural flood loads.
“The beauty of the truss bridge is that you don’t lose the clearance over the waterway; you don’t impede on water flows underneath,” Matt Stokes said.
“For this creek there’s a whole lot of nothing followed by high flows, it’s not a bad one for us because it disperses over a good spread, but to cope with that high influx of water coming through which usually carries debris with it you don’t want it catching on foundations of the bridge and blocking up the creek,” Mr Stokes said.
“We’ve built a dozen or so single span bridges with Wagners CFT now and this Collinsville Bridge is not our longest overall, but it is our longest riveted FRP truss bridge and a very simple one for us,” he said.
Pictured – Aerial view of the site of the bridge on Scottsville Road in Collinsville near the lawn bowls club.
Pictured – The new FRP bridge replaced an old metal bridge that had been decommissioned.