Waterfront moorings for sports yachts and cruisers of the Gold Coast glitterstocracy are set to be revolutionised with a new state of the art marine pile designed to reduce impact on berthing yachts.
Wagners Composite Fibre Technologies (CFT) have designed and manufactured the new Trident Marine Pile from pultruded Fibre Reinforced Polymer (FRP) and coated with a High Density Poly Ethylene (HDPE) outer sleeve.
Global Business Development Lead Michael Kemp said the natural modulus of elasticity, characteristic of FRP, allowed design engineers to develop a product that was strong and robust enough to withstand the marine environment, but giving enough to yield if a shipmaster came into dock too fast.
“Wagners’ 301 Trident Marine Piles bring all the benefits of high strength composites but have a lower stiffness than steel so they do flex more than their steel, or concrete counterparts,” Michael Kemp said.
“This makes them the perfect solution for the discerning skipper who has invested in a quality sports yacht or cruiser and wants to reduce impact on the vessel at docking,” Mr Kemp said.
“In fact, the Wagners Trident Marine Piles have the same stiffness as equivalent sized timber piles, whilst being a fraction of the weight, giving all the benefits of timber piles with dramatically improved durability,” he said.
“This technology will absolutely revolutionise marine structures, especially in that canal-river waterfront property setting; and because Wagners is an Australian owned and based manufacturer we’re ready to meet demand quickly.”
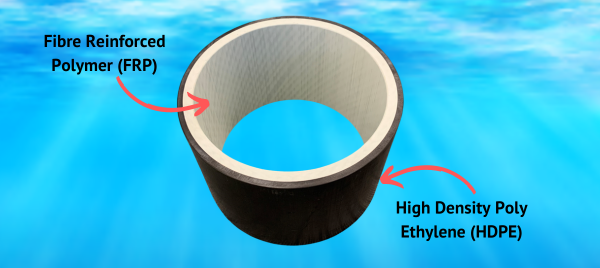
Photo – Wagners CFT’s new Trident Marine Pile is manufactured from pultruded Fibre Reinforced Polymer (FRP) and coated with a High Density Poly Ethylene (HDPE) outer sleeve.
Wagners’ FRP Trident Marine Piles also boast a host of other characteristics that lend to the product’s long-term sustainability and decreased maintenance costs over the lifetime of a structure.
“There’s so many other attributes of FRP that make it the perfect material for use in the marine environment; firstly FRP is chemically inert so it just won’t rust, rot or corrode in the salt water or harsh sunlight and it’s not affected by borers which is the number one destroyer of timber marine structures worldwide,” Michael Kemp said.
“Fibre Reinforced Polymer (FRP) is durable and we expect Wagner’s Trident Marine Piles and the accompanying FRP decking, gangways and stairs to achieve a 50-year design life with significantly reduced maintenance required,” Mr Kemp said.
“FRP is also non-leaching which means it is safe to use in marine areas of high conservation value; Plus Wagners CFT has recently published its Environment Product Declaration which is third-party verified and internationally recognised and can be used to determine how much embodied carbon you save with structures built from Wagners’ FRP,” he said.
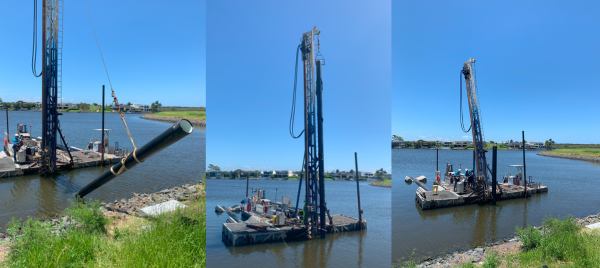
Photo – There are added benefits from a safety perspective with Trident Marine Piles being a quarter of the weight of a traditional steel marine pile including improved safety and ease of installation,
Marine structures have evolved over thousands of years and FRP is the latest modernised material taking marine structures by storm.
“Thousands of years ago marine structures were made from timber and stone; this graduated over time to steel which was found to inherently rust in marine environments,” Michael Kemp said.
“Then concrete was introduced and most of the concrete piles we see around the place are spun so they crack and corrode which lead the industry to relook at steel piles with a HDPE sleeve; and of course that evolved to FRP piles with the HDPE sleeve because in many previous examples the structural member corroded in the salt water before the intended design life was achieved,” Mr Kemp said.
“That’s where Wagners CFT can really shine because we’ve been making structural elements that are resistant to corrosion for more than 20 years; and up until this point our main hurdle with FRP marine piles was ensuring the movement of floating walkways and roller attachments didn’t impact the coating,” he said.
“The Trident Marine Piles have an integral HDPE sleeve over the FRP pile which ensures the integrity of the coating is maintained at all times.”
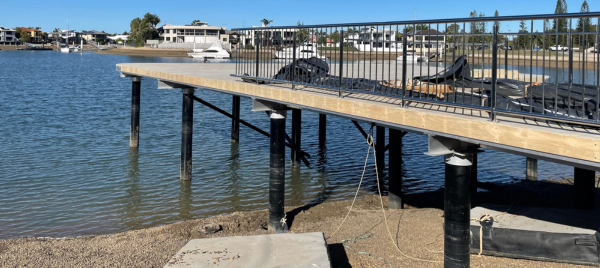
Photo – Wagners CFT’s new Trident Marine Piles being used at Newport Marketplace, north of Redcliffe Peninsula.
Owing to the lightweight nature of FRP, Trident Marine Piles can be installed utilising existing equipment with minimal modifications.
“Trident Marine Piles would be a quarter of the weight of a traditional steel marine pile, so you’ve got all the added benefits during installation from a safety perspective too,” Michael Kemp said.
“That includes less wear and tear on equipment, less risk for staff, reduced installation costs because you can move more, store more, faster and easier,” Mr Kemp said.
“They can be impact or vibratory driven into the substrate and because they are lighter, smaller pile drivers can be used; and because smaller pile drivers can be used, smaller floating jetties will also allow you to get into tighter spaces,” he said.
“And all your normal bolt ons are 100% compatible so you can utilise Wagners’ normal gangways, boardwalks, bridges and bolt it all straight on as a floating structure giving you a 100% FRP solution; including light poles.”
Wagners’ FRP 301 Trident Marine Piles are available worldwide and lead time can be as short as one month from order to delivery.
If you’d like to know more about Wagners’ FRP 301 Trident Marine Piles or you’d like to discuss an upcoming project reach out to your local Business Development Manager to organise a project deep dive https://www.wagner.com.au/contact-us/