Declining quality, rising prices and shortages of hardwood timber has led to major repair works being completed with modern composite materials at Southend Jetty in South Australia.
The jetty, located on the Limestone Coast near Beachport, is managed by the Department for Infrastructure and Transport (DIT) and is home to a significant rock lobster fleet.
DIT Manager of Marine Assets Spiros Dimas said Southend Jetty was built a long time ago, predominantly from timber and designed in an ‘L’ shape to get out to the deep water.
“Southend Jetty has been there since about the 60’s or 70’s and like all of the historic jetties in this area it is well designed, constructed from quality timber and because South Australia doesn’t have the beauty of deep harbours, was designed to chase the deep water allowing clippers and ships to drop off and pick up cargo,” Spiros Dimas said.
“All of these jetties are historical structures that have stood the test of time; some were even designed to take heavy industrial steam trains,” Mr Dimas said.
“But the tide has turned and we can’t depend or rely on timber for the repair of these jetties anymore because the quality is just not there, we don’t have the funding and even if we did, demand is so high we just can’t get our hands on the stock we need,” he said.
“Composite plastic is a solution for us.”

Photo – Southend Jetty in South Australia is located on the Limestone Coast near Beachport and is home to a significant rock lobster fleet.
Following a series of storms in 2021 Southend Jetty’s lower landings were damaged; with repairs to four lower landings and the removal and replacement of two others completed in December 2023 using Wagners Composite Fibre Technologies (CFT), Fibre Reinforced Polymer (FRP) structural profiles.
“We’d been doing band aid repairs on the lower landings for some time and it just got to the point where there was no point in trying to band aid any longer,” Spiros Dimas said.
“So I was on the search for the ultimate material that I could use in my marine facilities that gave me reduced cost for the structure’s whole life and something that would be maintenance free for the first 20 years,” Mr Dimas said.
“With timber you can complete repairs and within months your back replacing boards because it’s had a fungal or white ant attack, or its shrunk; I wanted to be able to put a plank there and have it stay there,” he said.
“So the repairs on Southend Jetty is a prototype of the lower landing design for us using composites for the jetty girders; we’re hoping to see the strength in UV, I want no to low maintenance and significantly reduced ongoing failures; and I want to come back in a month’s time and for the jetty to look as good then as it does today.”
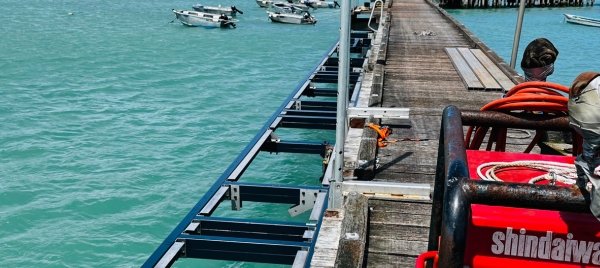
Photo – The lower landings of Southend Jetty are 1.8m wide, supported by FRP outriggins and cantilevered out under the proper with intermediary poles to lesser the spans by half and longitudinal girders and fenders.
Engineering firm, WGA (Wallbridge Gilbert Aztec) were engaged to develop the repair strategy for Southend Jetty and incorporate FRP into the design.
Marine Structures Engineer Uddish Singh said Southend was a really interesting project for WGA.
“We’ve done a decent amount of hybrid marine structures especially in the light weight category but the big thing with Southend for us was its importance to the local community,” Uddish Singh said.
“The community just revolves around this structure and even though its a fairly small town, the jetty is a lifeline for them from a tourist perspective; the local people are on the jetty almost every day and as an asset, we wanted to make sure that it was functional and working well for them,” Mr Singh said.
“Because these landings are semi-submersible and just above the level of the water, we needed to consider installation around tidal zones and timing; so we knew making everything as modular as possible was important,” Mr Singh said.
“Our client wanted something that was highly durable, able to be incorporated into the existing timber structure, low in maintenance and cost effective; so when you factor in everyone’s needs the materials you choose and the design you go with is a trade off,” he said.
“With FRP we were going to be able to achieve great strength; its lightweight so craning it on site and constructing modular sections to lift into place was going to work and it performs very well in marine environments, even semi-submersed.”
“The e-modulus of FRP is so much lower than steel, it does flex a bit more so we had to optimise the design to get the modulus to work and transfer the load path of the lower landings into existing piles on the jetty.”
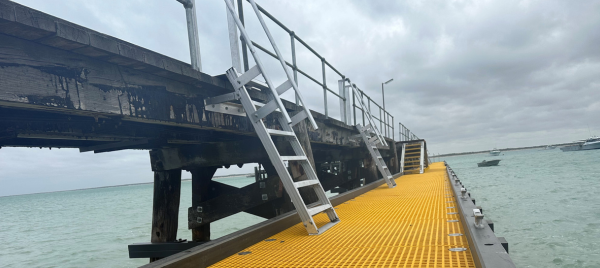
Photo – Wagners Fibre Reinforced Polymer (FRP) was chosen because the Department for Infrastructure and Transport wanted something that was highly durable, able to be incorporated into the existing timber structure, low in maintenance and cost effective to build and maintain.
The lower landings are 1.8m wide, supported by FRP outriggings and cantilevered out under the proper with intermediary poles to lesser the spans by half and longitudinal girders and fenders.
“We’re wrapped with the result and look forward to seeing how it performs as a prototype to roll out in other lower landings across the state,” Spiros Dimas said.
“From a safety and workability perspective, composites are much easier to man handle, modular and drop and bolt; they’re not big and heavy like hardwood timber and awkward to move around,” Mr Dimas said.
“We’ve been able to retro-fit an existing structure and sometimes when you do that you have to be a bit smart about matching it up,” he said.
“We made a commitment years ago to innovate and look to better ways of doing things and certainly composites are ticking boxes from the perspective of providing readily available resources that offer long-term life expectancy and reduced maintenance costs.”
“Additionally our next real issue to consider is decarbonising our structures and I’ve introduced carbon into my forecasting and modelling; so certainly we are very interested in understanding and harnessing the performance of FRP in helping to reduce global warming as well.”
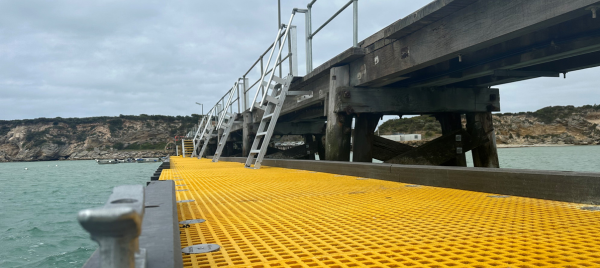
Photo – FRP is much easier to man handle, can be modular by design and provides efficiencies during installation with drop and bolt technology. FRP is not big and heavy like hardwood timber nor awkward to move.
Wagners FRP is the perfect solution for timber jetty rehabilitation because it is:
- Durable – with an expected 50-year design life.
- Chemically inert – will not rot, rust or corrode in salt water or UV radiation
- Resistant to marine borers, acid sulfate soils and termites
- Non leaching – perfect for areas of high-conservation value and marine life
- Lightweight and modular in design for safe and easy installation
- Cost effective – reduced maintenance and replacement cycles
For a copy of Wagners Environmental Product Declaration (EPD) visit sp10246-wagners-epd-pultruded-gfrp_nov23.pdf
To watch an on demand webinar that teaches you how to use Wagners EPD visit https://youtu.be/KJZQOwF89RA?si=QJEwZtEXo3IFx7tb
For more details on Timber Rehabilitation using Wagners CFT FRP visit timber-rehab-australasia-hi-def-pdf.pdf (wagner.com.au)
To get in contact with your local Business Development Manager and discuss rehabilitating a timber structure visit our contact page.